Betrieblicher Umzug von Schwermaschinen und Spezialmaschinen
Facility Management: Umzugsmanagement » Strategie » Doppelbetrieb » Industrie

Betrieblicher Umzug von Schwermaschinen und Spezialmaschinen
Der betriebliche Umzug von Schwermaschinen und Spezialmaschinen – etwa CNC-Fräsen, Pressen, Spritzgussmaschinen oder Härtereianlagen – ist ein hochkomplexer Prozess. Darunter versteht man die Verlagerung von industriellen Maschinen und Anlagen von einem Standort zu einem anderen, was sorgfältige Planung und Durchführung erfordert, um die Maschinen sicher zu transportieren und am neuen Ort wieder in Betrieb zu nehmen. Diese Art von Projekt stellt gleichzeitig strategische, logistische, technische und personelle Herausforderungen dar. Es genügt nicht, eine Maschine physisch von A nach B zu bewegen – vielmehr müssen alle Phasen von der Initiierung bis zur Nachsorge präzise koordiniert werden. Ziel ist es, Ausfallzeiten zu minimieren, Schäden zu vermeiden und die Produktion so schnell wie möglich wieder auf dem vollen Leistungsniveau laufen zu lassen. Von der initialen Projektplanung über die Demontage, den Transport bis zur Wiederaufstellung und Nachsorge müssen alle Schritte ineinandergreifen. Jede Phase bringt spezifische Herausforderungen mit sich, die durch Best Practices und Einhaltung einschlägiger Normen adressiert werden können.
Besonders hervorgehoben wurden die Themen Produktionssicherung und Liefertreue: Durch Maßnahmen wie Parallelbetrieb, Pufferproduktion und straffes Timing lässt sich die Ausfallzeit minimieren und die Versorgung der Kunden weiterhin gewährleisten. Praxisbeispiele belegen, dass mit exzellenter Planung selbst umfangreiche Verlagerungen unter laufender Produktion und mit minimalem Stillstand je Maschine realisierbar sind. Voraussetzung dafür ist allerdings eine detaillierte Planung jedes Arbeitsschritts und eine enge Kommunikation aller Beteiligten – Hersteller, Dienstleister, Mitarbeiter und Management ziehen idealerweise an einem Strang. Ein zentrales Erfolgskriterium ist zudem das Risikomanagement. Indem man mögliche technische, zeitliche und sicherheitsrelevante Risiken früh erkennt und Gegenmaßnahmen vorbereitet, wird das Projekt robust gegenüber Störungen. Qualitätssicherung in jedem Schritt – sei es durch Checklisten, Kalibrierungen oder Abnahmeprotokolle – gibt die nötige Sicherheit, dass die Maschine am neuen Standort wieder die erwartete Leistung bringt. Die Vorteile eines professionell durchgeführten Maschinenumzugs sind evident: Minimierte Ausfallzeiten, Kostenersparnis durch Vermeidung von Schäden, hohe Sicherheit und Zuverlässigkeit sowie eine kontinuierliche und effiziente Betriebsfortführung. Gleichzeitig erhöht ein solcher Umzug die Flexibilität des Unternehmens, z. B. um auf Marktveränderungen oder Standortvorteile zu reagieren, ohne in neue Maschinen investieren zu müssen.
Er ist ein Change-Prozess im Unternehmen. Gelingt er, so bewirkt er oft Verbesserungen – etwa ein optimiertes Layout, modernisierte Infrastruktur, eventuell ein technisches Retrofit der Maschine im Zuge des Umzugs – und sendet ein Signal für die Leistungsfähigkeit der Organisation. Misslingt er, drohen Produktionsverluste, Qualitätsprobleme und Vertrauensverlust bei Kunden.
- Projektplanung
- Produktionssicherung
- Maschinen
- Transport
- Wiederaufstellung
- Nachsorge
- Risikomanagement
- Normen
Projektplanung und -organisation
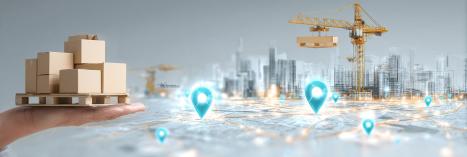
Jeder Maschinenumzug beginnt mit einer gründlichen Projektinitiierung und -planung. In dieser frühen Phase werden die Ziele und Rahmenbedingungen festgelegt: Welche Maschinen sollen wohin verlagert werden, warum erfolgt der Umzug (z. B. Werksverlagerung, Kapazitätserweiterung, Optimierung von Materialflüssen) und bis wann muss die Produktion wieder voll anlaufen? Bereits hier ist eine interdisziplinäre Planung erforderlich, die alle Beteiligten einbezieht – vom Produktionsmanagement über die Instandhaltung und Arbeitssicherheit bis hin zu Logistikexperten und externen Spezialisten für Maschinenmontage. Eine Projektorganisation mit klar definierten Rollen (Projektleitung, Teilprojektleiter für z. B. Demontage/Remontage, Logistikkoordinator etc.) wird etabliert, um Verantwortlichkeiten und Kommunikationswege festzulegen.
Ein Schwerpunkt der Planungsphase liegt auf der Detailplanung des zeitlichen Ablaufs. Für jede Maschine bzw. Anlage wird ein genauer Zeitplan erstellt, der Demontage, Transport, Wiederaufbau, Anschluss und Inbetriebnahme enthält. Zeitkritische Schritte – etwa das Verladen von besonders schweren Komponenten mittels Kran – werden als Meilensteine hervorgehoben, da Verzögerungen hier den gesamten Ablauf beeinträchtigen könnten. Moderne Projektmanagement-Methoden (z. B. Gantt-Diagramme, Netzplantechnik) helfen, Ablaufpläne übersichtlich zu gestalten und kritische Pfade zu identifizieren. Oft sind die Zeitfenster eng gesteckt, insbesondere wenn die Produktion nur kurze Zeit unterbrochen werden darf. So zeigen Praxisbeispiele, dass Maschinenumzüge häufig in präzise abgestimmten Etappen erfolgen müssen – etwa in Wochenblöcken – um den Betrieb nicht länger als nötig zu stören. Hierbei ist eine exakte Planung und Koordination nötig, damit die täglichen Umfänge an umzuziehenden Maschinen und die vorgegebenen knappen Zeitlimits exakt eingehalten werden können.
Parallel zur Terminplanung erfolgt die Ressourcenplanung. Es wird ermittelt, welche Fachkräfte (Mechaniker, Elektriker, Steuerungstechniker etc.) in welcher Anzahl benötigt werden und wann sie bereitstehen müssen. Gegebenenfalls sind externe Dienstleister für Schwertransporte oder Spezialmontagen frühzeitig zu beauftragen. Ebenso müssen Hilfsmittel und Equipment reserviert werden, z. B. Kräne mit ausreichender Tragkraft, Schwerlaststapler, Hubwagen, Schwerlastrollen, mobile Hebebühnen oder sogar hydraulische Hebeportale für das Anheben sehr schwerer Maschinen. Ein Beispiel verdeutlicht dies: Bei der Verlagerung von 292 Produktionsanlagen eines Elektronikfertigers wurde der Einsatz von bis zu 14 Monteuren parallel geplant sowie diverser Flurförderzeuge (2,5–8 t Gabelstapler), Scherenbühnen, ein Ladekran, Schwerlastfahrwerke, Hubwagen und Aluminium-Portalkräne – all dies musste just-in-time koordiniert bereitstehen. Auch die Versorgung mit nötigen Ersatzteilen oder Verbrauchsmaterialien (z. B. Dichtungen, Schmierstoffe, Verschraubungselemente) wird in der Planungsphase sichergestellt, um während des Umzugs keine unerwarteten Materialengpässe zu erleben.
Ein weiterer Aspekt ist die technische Bestandsaufnahme im Vorfeld. Für jede Maschine werden die technischen Unterlagen gesichtet: Aufstellpläne, Fundamentpläne, Schaltpläne, Stücklisten und Dokumentationen der Versorgungsanschlüsse. Diese Informationen fließen in ein Demontage- und Remontagekonzept ein. Gegebenenfalls sind Herstellerangaben zu berücksichtigen, insbesondere bei empfindlichen Spezialmaschinen – zum Beispiel können CNC-Fräsmaschinen oder Messmaschinen empfindlich auf Erschütterungen reagieren, was besondere Transportauflagen bedingt. In der Planung wird auch geprüft, ob Umbauten oder Anpassungen erforderlich sind: Muss am neuen Standort ein Fundament vorbereitet oder verstärkt werden? Sind die Hallentore groß genug für den Transport der Maschine? Müssen Kräne oder Hebegeräte bereitgestellt werden, um die Maschine an ihren neuen Platz zu heben? Solche Schnittstellen zwischen Bau, Infrastruktur und Maschine gilt es frühzeitig abzuklären. Häufig werden bereits in dieser Phase Genehmigungen eingeholt – z. B. behördliche Ausnahmegenehmigungen für Schwertransporte auf öffentlichen Straßen, oder interne Freigaben für das Abschalten von Versorgungsmedien (Strom, Druckluft) zu bestimmten Zeiten.
Nicht zuletzt beinhaltet die Projektplanung auch ein Kommunikations- und Stakeholder-Management. Es ist entscheidend, alle relevanten Stellen rechtzeitig ins Boot zu holen. Lieferanten müssen über veränderte Lieferadressen oder Anlieferungsfenster Bescheid wissen, Kunden über eventuelle produktionsbedingte Verzögerungen informiert werden, und interne Abteilungen wie Produktion, Qualitätsmanagement, IT und Arbeitssicherheit müssen in die Planung eingebunden sein. Regelmäßige Projektmeetings und Abstimmungsrunden ermöglichen es, die Anliegen aller Stakeholder zu berücksichtigen und einen reibungslosen Ablauf zu gewährleisten. Die Erfahrung zeigt, dass gute Kommunikation ein Schlüssel zum Erfolg solcher Projekte ist. In einem dokumentierten Fall wurde der genaue Ablauf vorab gemeinsam mit der Produktionsleitung durchgesprochen, sodass alle Beteiligten genau wussten, welche Maschinen in welchem Zeitraum verlagert werden und worauf zu achten ist. Durch diese permanente Abstimmung zwischen Umzugsteam und Produktion konnten Engpässe vermieden und das Projekt reibungsfrei durchgeführt werden.
Produktionssicherung und Parallelbetrieb
Die Sicherung der Produktion und Liefertreue während eines Maschinenumzugs hat oberste Priorität. Jede Stunde ungeplanter Stillstand kann enorme Kosten verursachen und Lieferketten stören. Um dies abzufedern, sind Strategien zur Produktionssicherung zu entwickeln. Ein zentrales Konzept ist dabei der Parallelbetrieb: Wo immer möglich, wird versucht, die Fertigung trotz laufendem Umzug aufrechtzuerhalten, sei es durch parallele Anlagen, Ausweichkapazitäten oder durch geschickte Sequenzierung der Umzugsschritte.
In der Praxis bedeutet dies zum Beispiel, dass Redundanzen genutzt oder geschaffen werden: Verfügt der Betrieb über mehrere ähnliche Maschinen, wird der Umzug einzelner Anlagen gestaffelt, sodass die restlichen Maschinen die Produktion vorübergehend übernehmen können. Ist nur eine einzelne Anlage vorhanden, planen viele Unternehmen Pufferproduktion ein, bevor der Umzug beginnt – es werden also ausreichende Vorräte an Halbzeugen oder Fertigprodukten produziert, um die Lieferfähigkeit während des Stillstands zu erhalten. Alternativ kann – falls möglich – auf Lohnfertiger oder Partnerunternehmen zurückgegriffen werden, die temporär die Produktion von Teilen übernehmen. Kommunikation mit Kunden ist hier ebenfalls essenziell: Bei langfristig avisierten Umzugsprojekten können Liefertermine proaktiv angepasst oder großzügigere Lieferfristen vereinbart werden, um Risiken für die Liefertreue zu reduzieren.
Eine weitere bewährte Maßnahme zur Produktionssicherung ist die Aufteilung des Umzugs in mehrere kurze Zeitfenster statt eines langen Stillstands. Beispielhaft sei ein Großprojekt genannt, bei dem knapp 300 Maschinen innerhalb eines Werkes umgezogen wurden, während die laufende Produktion weiterging. Der Kunde hatte eine maximal eintägige Stillstandszeit pro Maschine vorgegeben. Um dies zu erreichen, wurde der Gesamtumzug in fünf einwöchige Phasen unterteilt, die parallel zur laufenden Fertigung abliefen. Vor jeder Phase wurde exakt definiert, welche Maschinen in welchem Zeitraum verlagert werden, und am jeweiligen Tag X wurde die Maschine abends am alten Platz abgeklemmt und am nächsten Morgen am neuen Platz wieder in Betrieb genommen. Dieses Vorgehen erforderte eine außerordentlich gut geplante Logistiklösung und den intelligenten Einsatz von Personal und Technik, war jedoch erfolgreich und die Produktion konnte ohne nennenswerte Gesamtunterbrechung weiterlaufen. Das Beispiel zeigt, dass durch präzise Taktung und parallele Abläufe drastische Reduktionen von Stillstandszeiten möglich sind – allerdings nur unter der Voraussetzung, dass Planung und Ausführung absolut verlässlich sind.
Zeitkritische Schnittstellen treten vor allem dort auf, wo der Umzug mit anderen betrieblichen Abläufen kollidiert. Solche Schnittstellen können technische Natur sein (etwa das Abschalten der Stromversorgung in einem Zeitfenster, in dem der Restbetrieb darauf angewiesen ist) oder organisatorisch (Übergabe von Halbfertigteilen an einen anderen Standort). Um hier Risiken zu minimieren, werden oft Übergabeszenarien vorab definiert. Beispielsweise kann für den Zeitraum des Umzugs einer Spritzgussmaschine eine Parallelmaschine in einer anderen Werkshalle installiert werden, die zumindest einen Teil der Produkte weiterfertigt. Oder es werden temporäre Arbeitsplätze eingerichtet, z. B. manuelle Montagetische, um den Produktionsfluss aufrechtzuerhalten, während automatisierte Anlagen verlagert werden.
Auch die Mitarbeiter spielen beim Parallelbetrieb eine wichtige Rolle. Geplante Umzüge finden häufig an Wochenenden, Betriebsferien oder in Nachtschichten statt, um die reguläre Produktion so wenig wie möglich zu stören. Das Personal wird entsprechend eingeteilt und geschult, sodass klar ist, wer im Falle eines Parallelbetriebs welche Aufgaben übernimmt. Beispielsweise kann während des Abbaus einer Maschine das Bedienpersonal in anderen Bereichen aushelfen oder an der Wiederinbetriebnahme am neuen Standort mitwirken. Wichtig ist zudem, frühzeitig die IT-Systeme (z. B. MES, ERP) an die Übergangssituation anzupassen – etwa müssen Maschinen im System umgebucht werden, Aufträge ggf. auf andere Maschinen umgeleitet und Datenverbindungen (Netzwerk, Leitrechner) vorübergehend umkonfiguriert werden.
Letztlich dient all dies dem Ziel, die Lieferverpflichtungen und die Gesamtanlageneffektivität (OEE) möglichst wenig zu beeinträchtigen. Durch vorausschauende Planung lässt sich die Produktionsunterbrechung planbar machen und in engen Grenzen halten. Unternehmen mit zertifiziertem Qualitätsmanagement (z. B. nach ISO 9001) richten hierbei ihr Augenmerk besonders auf die Kundenanforderungen: Liefertreue ist ein wesentliches Qualitätskriterium, das es trotz interner Umstellungen zu erfüllen gilt. Es empfiehlt sich daher, Kennzahlen wie den Lieferterminerfüllungsgrad und Outputraten während eines Umzugs eng zu überwachen. Sollte es dennoch zu Engpässen kommen, können mit zuvor ausgearbeiteten Notfallplänen (Contingency Plans) Gegenmaßnahmen ergriffen werden – zum Beispiel kurzfristige Sonderschichten nach dem Umzug, um Produktionsrückstände aufzuholen.
Demontage der Maschinen und Anlagen
Die Phase der Demontage markiert den praktischen Start des Umzugs und muss äußerst sorgfältig durchgeführt werden. Sie beginnt mit vorbereitenden Maßnahmen direkt an der Maschine im laufenden Betrieb, sobald die Produktion freigegeben ist. Zunächst werden alle Versorgungsmedien kontrolliert heruntergefahren und gesichert: Elektrische Anschlüsse werden spannungsfrei geschaltet (Stichwort Lockout-Tagout, in Deutschland das Abschließen und Kennzeichnen von Schaltern), Druckluft- und Hydrauliksysteme werden drucklos gemacht, Zuführungen von Wasser, Gas oder Kühlmitteln werden abgestellt und entleert. Bei vielen Maschinen – insbesondere CNC-Werkzeugmaschinen oder robotergestützten Anlagen – sind Daten ein kritischer Punkt: Alle Steuerungsprogramme, Parametrierungen und Kalibrierwerte der Maschine werden gesichert (Backup), um sicherzustellen, dass nach dem Wiederaufbau keine Informationen verloren gegangen sind. Dies umfasst auch das Sichern von Maschineneinstellungen und ggf. NC-Programmen oder Rezepturen bei prozessgesteuerten Anlagen.
Ein weiterer Vorbereitungsschritt ist die Fixierung beweglicher Teile. Große Maschinen enthalten oft Achsen, Tische oder Köpfe, die beim Transport verrutschen oder durch Schwingungen beschädigt werden könnten. Diese werden durch Transportsicherungen arretiert (z. B. mechanische Klemmen, Spannbänder oder spezielle Transportsicherungssets vom Hersteller). Gegebenenfalls müssen auch Pufferbatterien von Steuerungen vor dem Abklemmen getauscht oder gepuffert werden, um den Erhalt von Speicherinhalten zu gewährleisten. Parallel dazu wird die Demontage systematisch dokumentiert: Jedes abgebaute Teil, jedes Kabel und jeder Schlauch werden so gekennzeichnet, dass beim Wiederaufbau Verwechslungen ausgeschlossen sind. In einem Demontageprotokoll wird festgehalten, welche Baugruppen in welcher Reihenfolge demontiert wurden, welche Schrauben/Schnittstellen wohin gehören und welcher Zustand vor dem Abbau herrschte. Fotos und Markierungen (z. B. farbige Labels an Kabeln und Anschlüssen) sind hier unerlässlich, um später eine reibungslose Remontage sicherzustellen.
Die fachgerechte Demontage selbst erfolgt nach den geplanten Schritten: Zuerst werden periphere Einrichtungen abgebaut (Schutzzäune, Verkleidungen, Zuführbänder etc.), dann Versorgungsleitungen und Schnittstellen getrennt, schließlich die Hauptbaugruppen der Maschine zerlegt. Dabei ist unbedingt auf die Herstellervorgaben zu achten – moderne Maschinen haben definierte Hebepunkte und Demontageabfolgen, um Strukturschäden zu vermeiden. Es kommen geeignete Hebezeuge zum Einsatz, um schwere Komponenten zu bewegen, z. B. Hallenkräne, mobile Kransysteme oder Gabelstapler mit speziellen Anschlagmitteln. Schon bei der Demontage wird die Verpackung für den Transport mitgedacht: Abgebaute Teile werden direkt auf passende Paletten oder in Kisten gelegt, mit Polstermaterial geschützt und fixiert. Besonders empfindliche Teile (Elektronik, Messsysteme, Glas, feine Mechanik) erhalten spezielle Verpackungen – manchmal werden Klimakisten oder Stickstoffverpackungen genutzt, um Korrosion oder Feuchtigkeitsschäden während Transport oder Zwischenlagerung zu verhindern.
Ein wichtiger Teil der Demontagephase ist auch die Arbeitssicherheit. Die Demontage einer großen Maschine bringt erhebliche Risiken mit sich: schwere Teile in Bewegung, mögliche Restenergien in Hydraulik oder Federn, scharfe Kanten, herausragende Teile. Daher müssen alle Beteiligten gemäß den Arbeitsschutzvorschriften unterwiesen und mit persönlicher Schutzausrüstung (PSA) ausgestattet sein (Helm, Sicherheitsschuhe, Handschuhe, ggf. Schutzbrille und -kleidung). Absturzsicherungen sind bei Arbeiten in höher gelegenen Bereichen Pflicht. Lasten werden nur innerhalb der zugelassenen Tragfähigkeiten gehoben; Lastaufnahmemittel und Anschlagpunkte werden vorab geprüft. Zudem sollte für den Fall unvorhergesehener Ereignisse (z. B. ein verklemmter Maschinenteil, ein abgestürzter Gegenstand) ein Notfallplan bereitliegen. Die Demontage wird idealerweise von einem erfahrenen Montageteam durchgeführt, das mit der betreffenden Maschinenart vertraut ist. In einigen Fällen empfiehlt es sich, Servicetechniker des Maschinenherstellers hinzuzuziehen – etwa wenn spezielle Kenntnisse oder Werkzeuge erforderlich sind, um z. B. eine CNC-Spindel fachgerecht auszubauen oder eine Presse mechanisch zu entspannen.
Nachdem alle Teile der Maschine abgebaut und verpackt sind, wird der Maschinenstandort am alten Platz geräumt. Jetzt bietet sich oftmals die Gelegenheit, verbliebene Fundamentreste zu entfernen oder den Platz für eine neue Maschine vorzubereiten, falls es sich um eine Umzugs- bzw. Austauschaktion handelt. Manchmal wird der alte Standort zeitnah für andere Zwecke genutzt, was in der Planung berücksichtigt sein muss (z. B. umgehende Aufbereitung des Bodens, Versetzen von Anschlüssen). Der abgebauten Maschine hingegen steht nun der Transport bevor – intern zur Laderampe und extern zum neuen Bestimmungsort.
Transport und Logistik
Die Logistik des Maschinenumzugs gliedert sich in zwei Teile: den innerbetrieblichen Transport (das Bewegen der demontierten Maschine innerhalb des Werks bzw. zum Verladepunkt) und den außerbetrieblichen Transport (Speditions- bzw. Schwertransport zum neuen Standort). Beide Abschnitte bringen spezifische Herausforderungen mit sich, insbesondere bei Schwergut und Großdimensionen.
Innerbetrieblich müssen oft beengte Platzverhältnisse und begrenzte Tragfähigkeiten berücksichtigt werden. Schwerlastmaschinen wie Pressen oder Spritzgussanlagen können mehrere Dutzend Tonnen wiegen; hier ist zu prüfen, ob der Hallenboden und eventuell beteiligte Aufzüge oder Zwischenböden diese Last tragen können. Falls nicht, müssen temporäre Verstärkungen (z. B. Stahlplatten zur Lastverteilung) oder alternative Routen (z. B. Durchbruch einer Wand statt Transport durch ein Tor) eingeplant werden. Für den horizontalen Transport kommen Schwerlastrollen und Fahrwerke zum Einsatz. Diese kleinen, rollenbasierten Plattformen können unter schwere Maschinenteile gesetzt werden, um sie per Muskelkraft oder Zuggerät zu bewegen. Auch Gabelstapler mit hoher Traglast (teilweise Spezialstapler mit 10+ Tonnen Kapazität) werden eingesetzt, sofern genügend Rangierfläche vorhanden ist. Der vertikale Transport – z. B. das Absenken von Maschinenteilen von einem Fundament oder das Aufnehmen auf einen Tieflader – erfolgt meist mittels Kran. In Hallen kommen Brückenkräne oder bei Bedarf mobile Autokrane zum Einsatz, die in die Halle fahren oder von außen durch Dachöffnungen/Tore heben. Eine weitere Option sind hydraulische Hubportale, die besonders bei sehr schweren Lasten (über 50 Tonnen) verwendet werden: Dabei wird ein Gerüst um die Last aufgebaut, das diese mit Hydraulikzylindern langsam anheben und absenken kann. All diese Schritte erfordern eine exakte Logistikplanung – also die richtige Reihenfolge der Bewegungen, Bereitstellung der Geräte zum richtigen Zeitpunkt und Absicherung der Transportwege.
Für den externen Transport (zwischen altem und neuem Standort) sind die Anforderungen noch vielfältiger. Handelt es sich um einen Umzug auf dem gleichen Werksgelände oder in unmittelbarer Nähe, kann oft mit betriebseigenen Mitteln (Stapler, Zugmaschinen) gearbeitet werden. Sobald jedoch öffentliche Straßen genutzt werden, greift das Reglement für Schwertransporte und Spezialtransporte. In Deutschland (und ähnlich in Europa) ist ein Schwertransport in der Regel gegeben, wenn ein beladenes Fahrzeug bestimmte Maße oder Gewichte überschreitet (z. B. Gesamtgewicht > 40 t, Breite > 3 m, Höhe > 4 m, Länge > 20 m, oder Achslastgrenzen). Viele Maschinen – insbesondere große CNC-Bearbeitungszentren oder Anlagenrahmen – überschreiten diese Limits und müssen daher auf speziellen Tiefbettaufliegern oder modularen Schwerlasttrailern transportiert werden. Für solche Transporte sind behördliche Genehmigungen erforderlich, oft unter Auflagen wie Fahrzeitbeschränkungen (Nacht- und Wochenendfahrten), Begleitfahrzeugen (BF3/BF4 mit Warnkennzeichnung) und gegebenenfalls Polizeibegleitung. Die Route wird im Voraus geplant und von den Behörden geprüft: Es müssen ausreichend breite Straßen und Kurvenradien vorhanden sein, Brücken müssen die Last tragen (ggf. müssen Brückenbefahrungen genehmigt werden), und Hindernisse wie niedrige Unterführungen oder Baustellen sind zu berücksichtigen. Mitunter werden Ampeln angehoben oder temporär Hindernisse demontiert, damit ein sperriges Maschinenteil passieren kann.
Ein zentraler Aspekt ist die Ladungssicherung nach geltenden Normen. Schwere Maschinenteile müssen auf dem Transportfahrzeug so befestigt werden, dass sie auch bei Bremsmanövern oder Straßenvibrationen nicht verrutschen oder Schaden nehmen. Hier kommen z.B. die VDI-Richtlinie VDI 2700 (Ladungssicherung auf Straßenfahrzeugen) und DIN-Normen zur Verzurrung zum Tragen. Es werden Zurrgurte, Ketten, Spannvorrichtungen und rutschhemmende Matten eingesetzt, teils auch spezielle Transportgestelle, in denen Maschinenteile formschlüssig eingespannt werden. Empfindliche Geräte können zusätzlich mit Stoßsensoren versehen werden, um Erschütterungen aufzuzeichnen – so lässt sich später nachvollziehen, ob z. B. ein CNC-Bearbeitungszentrum während des Transports Schocks ausgesetzt war, die eine Nachkalibrierung erfordern.
Bei internationalen Umzügen (z. B. Verlagerung ins Ausland) kommen weitere logistische Komponenten hinzu: der Seetransport in Containern oder als Schwergut (mit Kranverladung in Häfen), eventuell Luftfracht für eilige kleinere Maschinenkomponenten, sowie Zoll- und Exportdokumentation. In solchen Fällen sind Verpackungen gemäß Seefrachtstandard (luftdicht verschweißte Folien mit Trockenmittel gegen Seeluft-Korrosion, stabile Kisten nach IPPC-Standard für Holz) nötig. Die Planung muss hier die längere Transportzeit und mögliche Verzögerungen (z. B. durch Zollabfertigung) einbeziehen. Wichtig ist auch die Transportversicherung: Hochwertige Maschinen werden in der Regel separat versichert, um Transportschäden finanziell abzudecken. Versicherer verlangen oft Nachweise über fachgerechte Verpackung und Ladungssicherung – ein weiterer Grund, diese Aspekte streng nach Norm auszuführen.
Parallel zum physischen Transport ist stets die Logistikkette im Auge zu behalten. Das bedeutet, am neuen Standort müssen zum Eintreffen der Maschine alle Voraussetzungen erfüllt sein: Entladeequipment (Kran, Stapler) bereit, Aufstellungsplatz zugänglich (die Baustelle muss frei sein), Aufstellfläche tragfähig und markiert, Montagepersonal anwesend. Ein Knackpunkt kann etwa sein, wenn ein Tieflader nachts ankommt, aber der Hallenkran erst am Morgen bedient werden kann – solche Situationen gilt es in der Planung zu vermeiden, ggf. durch Pufferzeiten oder Bereithalten von Ausweichlösungen. Bei besonders kritischen Maschinen transportieren einige Unternehmen zusätzlich Servicetechniker oder Monteure mit, die während des Transports die Maschine begleiten und etwa für Zwischenstopps bereitstehen, um Kontrollen durchzuführen.
Wiederaufstellung und Inbetriebnahme
Am neuen Standort angekommen, durchläuft die Maschine den Prozess der Wiederaufstellung (Remontage) und Inbetriebnahme. Diese Phase ist ebenso kritisch wie die Demontage, da hier die Voraussetzungen geschaffen werden, dass die Maschine wieder einwandfrei produziert. Der erste Schritt ist das Einbringen der Maschinenteile an ihren neuen Aufstellungsort. Gegebenenfalls musste hierfür im Vorfeld baulich vorgesorgt werden, z. B. durch Fundamentarbeiten. Viele schwere Maschinen erfordern ein spezielles Fundament mit ausrechender Tragfähigkeit, Schwingungsdämpfung oder Verankerungen. Wenn ein neues Fundament gegossen wurde, muss dessen Aushärtung und Ebenheit geprüft sein, bevor die Maschine darauf montiert wird.
Die Remontage erfolgt im Prinzip in umgekehrter Reihenfolge zur Demontage, jedoch unter zusätzlichen Anforderungen: Alle Teile müssen präzise justiert und fest verbunden werden. Zunächst werden die Hauptbaugruppen positioniert – grob mittels Kran oder Stapler, feinjustiert dann mit Richtsätzen, Laser oder Messuhren. Bereits hier kommt kalibriertes Messwerkzeug zum Einsatz, um die Ausrichtung genau zu kontrollieren. Beispiel: Das Bett einer Werkzeugmaschine wird mit Nivelliergeräten (Präzisionswasserwagen oder elektronischen Neigungssensoren) ausgerichtet und mittels Gewindespindeln oder Unterlagsplatten justiert, bis es im Toleranzbereich (oft wenige Hundertstel Millimeter pro Meter) liegt. Danach werden Achsmodule, Anbauteile, Verkleidungen etc. in der vorgesehenen Reihenfolge montiert – stets mit Blick auf Parallelität, Rechtwinkligkeit und korrekten Abständen, wie von den Herstellerdaten vorgegeben.
Parallel dazu erfolgt die elektrische und medientechnische Installation. Alle zuvor gelabelten Kabelverbindungen werden entsprechend den Markierungen wieder angeschlossen, Pneumatik- und Hydraulikschläuche werden verbunden und entlüftet, Kühlmittel- und Schmieranlagen werden befüllt. Hierbei sind unbedingt die geltenden Anschlussnormen zu beachten, z. B. dass elektrische Installationen gemäß DIN EN 60204-1 (Maschinensicherheit – Elektrische Ausrüstung von Maschinen) erfolgen. Ein Aspekt ist die elektrische Sicherheit: Nach Abschluss der Verkabelung schreibt die DGUV Vorschrift 3 (ehemals BGV A3) eine Überprüfung der elektrischen Anlage vor. Diese Prüfung durch eine Elektrofachkraft umfasst Isolationsmessungen, Schutzleiterprüfungen und Funktionsproben der Sicherheitsschaltkreise, um sicherzustellen, dass keine Beschädigung beim Umzug die elektrische Sicherheit beeinträchtigt hat. Gerade Maschinen mit hohen Anschlusswerten (z. B. große Pressen oder Spritzgussmaschinen mit >100 kW Anschlussleistung) müssen sauber an die neue Elektroinfrastruktur (Schaltschränke, Transformatoren) angebunden werden. Oft wird in diesem Zuge auch die Netzqualität geprüft (Spannungspegel, Phasenfolge), insbesondere bei internationaler Verlagerung (Stichwort unterschiedliche Netzspannungen oder -frequenzen: 50 Hz vs. 60 Hz, was Transformatoren oder Umrichter erfordern kann).
Nach der mechanischen Montage und Verkabelung steht die Inbetriebnahme bevor. Sie beginnt mit einer Kaltinbetriebnahme: Das heißt, die Maschine wird zunächst eingeschaltet und durchläuft interne Selbsttests, ohne dass direkt produziert wird. Steuerungen und Software werden hochgefahren, Achsen ggf. referenziert. Nun zeigt sich, ob alle Komponenten korrekt verbunden sind – etwa ob Sensoren Signale liefern, Aktoren ansprechen und keine Fehlermeldungen auftreten. Treten hierbei Fehler auf, müssen sie systematisch behoben werden (z. B. vertauschte Steckverbindungen, Druckabfall in Hydraulik, Parametereinstellungen). Anschließend folgen Trockenläufe und Funktionsprüfungen: Die Maschine wird in Leerlauf oder Testmodus betrieben. Eine Werkzeugmaschine verfährt Achsen über den gesamten Weg zur Kontrolle der Wegmesssysteme; eine Presse wird einige Hübe im Leerzustand betrieben; eine Spritzgussmaschine fährt einzelne Zyklen ohne Material. Dabei werden sämtliche Funktionen auf korrekte Wirkung getestet, einschließlich Not-Halt und Schutzeinrichtungen (Lichtvorhänge, Zweihandschaltung etc.). Diese Sicherheitsfunktionen müssen wie bei einer Neuinstallation validiert werden, oft unter Zuhilfenahme der Betriebssicherheitsverordnung (BetrSichV) und ggf. externer Sachverständiger, falls es sich um prüfpflichtige Anlagen handelt (z. B. Druckbehälter in Härteanlagen oder kraftbetriebene Pressen können Abnahmeprüfungen erfordern).
Ein zentraler Schritt ist dann die Kalibrierung und Justierung der Maschine. Trotz aller Vorsicht können Transport und Wiederaufbau kleine Abweichungen verursacht haben. Daher werden Maschinen nach der Aufstellung erneut kalibriert. Bei CNC-Fräsmaschinen beispielsweise wird die geometrische Genauigkeit überprüft – mittels Laserinterferometern oder Präzisionsrichtleisten werden Positioniergenauigkeit und Geradheit der Achsen nach ISO 230 geprüft. Oft kommen sogenannte Ballbar-Tests zum Einsatz, um die Kreisformgenauigkeit des Maschinenlaufs zu testen. Bei Messmaschinen oder Prüfanlagen werden normgerechte Kalibrierungen nach ISO/IEC 17025 durchgeführt, um messtechnische Rückführbarkeit sicherzustellen. Andere Anlagen erfordern Prozesskalibrierungen: Eine Härterei-Anlage z.B. muss eventuell mit Thermoelementen neu vermessen werden, um Temperaturgleichförmigkeiten zu bestätigen. All diese Kalibrier- und Messprozeduren werden dokumentiert, um Prüfnachweise über die Maschinenfähigkeit am neuen Standort zu erhalten. So kann z. B. ein Kalibrierschein mit Dokumentation erstellt werden, der den Nachweis der Messmittelüberwachung nach ISO 9001 erbringt. Diese Dokumente sind wichtig für das Qualitätsmanagement und im Falle von Audits oder Kundenabnahmen.
Nach Abschluss von Kalibrierung und Trockenläufen erfolgt die Produktionsaufnahme im Beisein des verantwortlichen Fachpersonals. Meist wird zunächst eine Testproduktion durchgeführt: Die Maschine fertigt erste Teile unter realen Bedingungen, die intensiv vermessen und geprüft werden. Damit wird bestätigt, dass die Maschine genauso oder besser als zuvor produziert. Falls Abweichungen festgestellt werden (z. B. Maßhaltigkeitsprobleme, Oberflächengüteabweichungen), können noch Nachjustierungen vorgenommen werden. Erst wenn alle Kriterien erfüllt sind, wird die Maschine offiziell abgenommen. Diese Abnahme kann intern durch die Qualitätsabteilung erfolgen und/oder extern mit dem Kunden, falls die Maschine Teil eines Lieferauftrags ist. In regulierten Industrien (z. B. Pharma oder Medizintechnik) wird gegebenenfalls eine formale Re-Qualifizierung gefordert, d.h. eine erneute Installationsqualifizierung (IQ) und Funktionsqualifizierung (OQ) der Maschine am neuen Ort, um den Behördenanforderungen zu genügen.
Wesentlich für den Abschluss dieser Phase ist auch die Dokumentation: Alle durchgeführten Arbeiten, Prüfungen und Änderungen werden schriftlich festgehalten. Im Abschlussbericht des Umzugsprojekts wird vermerkt, wann die Maschine abgenommen wurde, welche Parameter eingestellt sind, wer die Freigabe erteilt hat und welche eventuell offenen Punkte noch zu beobachten sind. Zudem werden dem Betreiber die aktualisierten Dokumente übergeben – z. B. aktualisierte Schaltpläne, neue Kalibrierprotokolle und eine Liste an Wartungsempfehlungen oder nächsten Prüfterminen. Nicht selten schult das Montageteam oder der Hersteller noch einmal das Bedien- und Instandhaltungspersonal hinsichtlich aller relevanten Punkte, insbesondere wenn die Maschine am neuen Platz unter geänderten Bedingungen läuft (andere Umgebungseinflüsse, neues Peripheriesystem etc.). Sind alle diese Schritte erfolgreich absolviert, kann die Maschine in den Normalbetrieb übergehen.
Nachsorge und Abschluss des Projekts
Mit der formalen Abnahme und Wiederinbetriebnahme ist der Prozess noch nicht ganz abgeschlossen. In der Nachsorgephase wird der laufende Betrieb der umgezogenen Maschine in den ersten Tagen oder Wochen eng begleitet. Das Ziel ist, etwaige Anlaufschwierigkeiten früh zu erkennen und zu beheben. Die Praxis zeigt, dass nach einem großen Umzug gelegentlich Nachjustagen nötig sind – z. B. kann es sein, dass sich eine Maschine nach einigen Temperaturzyklen minimal setzt und neu nivelliert werden muss, oder dass bestimmte Sensorik erst im Realbetrieb feinjustiert werden kann. Daher bleibt das Projektteam oder zumindest ein Teil davon in Rufbereitschaft, um schnell eingreifen zu können. Manche Dienstleister bieten explizit eine Phase der Produktionsbegleitung an, bis eine definierte stabile Produktionsqualität erreicht ist.
Zudem werden in der Nachsorge Leistungsdaten überwacht: Läuft die Maschine auf den geplanten Taktzeiten? Erreichen die Qualitätskennzahlen (Ausschussrate, Nacharbeitsbedarf) wieder das alte Niveau? Werden alle sicherheitsrelevanten Checks (z. B. tägliche Sicherheitsprüfung einer Presse) ordnungsgemäß durchgeführt? Diese Überwachung in der Anfangsphase dient der Qualitätssicherung und dem Nachweis, dass der Umzug keinen negativen Einfluss auf die Produktionsleistung hatte – im Idealfall konnten durch Optimierungen im Zuge des Umzugs sogar Verbesserungen erzielt werden (z. B. kürzere Rüstzeiten durch neue Aufstellungsanordnung).
Ein wichtiger Teil der Projektabschlussphase ist auch das Lessons Learned: In einem Abschlussmeeting werden Erfahrungen und Erkenntnisse des Umzugsprojekts dokumentiert. Was lief gut, wo gab es Probleme, welche Empfehlungen gibt es für zukünftige Verlagerungen? Diese Informationen sind äußerst wertvoll, um kontinuierlich bessere Prozesse zu entwickeln. Unternehmen mit ISO 9001-Zertifizierung verankern solche Nachbetrachtungen oft im Verbesserungsprozess – z. B. in Form eines Abschlussberichts, der auch ins Dokumentenmanagement einfließt.
Aus formaler Sicht wird schließlich das Projekt offiziell beendet, z. B. durch ein vom Management unterzeichnetes Abnahmedokument oder eine Projektabschlusspräsentation. Verträge mit externen Dienstleistern werden abgeschlossen, und die Verantwortlichkeiten gehen zurück an die Linienorganisation (Produktionsleitung, Instandhaltung). Es sollte klar definiert sein, ab wann die Maschine wieder unter normale Wartungsverantwortung fällt und welche Garantie oder Gewährleistung der Umzugsdienstleister für seine Arbeit bietet. Manche Anbieter geben z. B. eine Gewährleistungsfrist auf Montageleistungen, innerhalb derer sie auftretende Mängel kostenlos beheben.
Risikomanagement und Qualitätssicherung
Angesichts der vielen Schritte und Beteiligten bei einem Maschinenumzug ist ein systematisches Risikomanagement unerlässlich. Bereits in der Planungsphase werden potenzielle Risiken identifiziert, bewertet und mit Gegenmaßnahmen versehen.
Risiken bestehen dabei in mehreren Kategorien:
Technische Risiken: Dazu zählen Beschädigungen an der Maschine (z. B. Verzug des Maschinenbetts durch falsches Heben, elektronischer Schaden durch unsachgemäße Trennung) oder Funktionsstörungen nach dem Wiederaufbau. Die Mitigation besteht hier in sorgfältiger technischer Planung, Einsatz von geeignetem Equipment, Befolgung von Herstellervorgaben und in zusätzlichen Prüfungen. Beispielsweise kann durch eine Strukturanalyse vorab sichergestellt werden, dass die Maschine die Belastungen des Transports aushält. Auch die Kalibrier- und Testprozeduren bei der Inbetriebnahme dienen dazu, technische Probleme früh aufzudecken.
Organisatorische Risiken: Hier geht es um Terminverzögerungen, Ressourcenengpässe oder Koordinationsprobleme. Ein typisches Risiko ist, dass der Zeitplan nicht hält – etwa durch Schlechtwetter beim Transport oder durch unvorhergesehene Probleme beim Abbau. Gegenmaßnahmen sind Pufferzeiten und ein kontinuierliches Monitoring des Projektfortschritts. Für kritische Transporte wird ein Plan B erarbeitet (etwa alternative Routen oder Ersatzkran bei Ausfall). Organisatorische Risiken adressiert man auch durch klare Verantwortlichkeiten und Kommunikationswege: Wenn z. B. eine kurzfristige Entscheidung nötig ist (Material defekt, Ersatzteilbeschaffung), muss klar sein, wer entscheiden darf und wie Informationen fließen. In dem geschilderten Beispiel mit der eintägigen Maschinen-Stillstandszeit war es entscheidend, dass Personal und Technik intelligent eingesetzt wurden und bei Bedarf schnell umdisponiert werden konnten.
Wirtschaftliche Risiken: Jeder Produktionsstillstand kostet Geld, ebenso wie mögliche Schäden, Eilfracht oder Vertragsstrafen bei Lieferverzug. Das Risikomanagement beziffert diese Kosten und stellt ihnen Präventionskosten gegenüber. Oft wird ein Risikopuffer im Budget eingeplant, typischerweise ein Prozentsatz der Projektsumme, um Unvorhergesehenes abzudecken. Zudem empfiehlt es sich, versicherungsseitig vorzusorgen: Eine Transportversicherung (Werks-Transport-Versicherung) deckt Schäden am Gut, eine Betriebsunterbrechungsversicherung kann extreme Ausfallschäden abfedern. Wichtig ist, dass die Versicherungssummen den potenziellen Schaden abdecken – gerade bei sehr teuren Spezialmaschinen (CNC-Anlagen können Millionenwerte haben) und hochgetakteter Produktion (Stillstandskosten von einigen zehntausend Euro pro Stunde sind in Automobil- oder Prozessindustrie keine Seltenheit). Studien zeigen, dass ungeplante Ausfallzeiten in Großunternehmen durchschnittlich sechsstellige Summen pro Stunde kosten können – dies unterstreicht die Notwendigkeit, das wirtschaftliche Risiko klein zu halten.
Regulatorische und sicherheitstechnische Risiken: Ein oft unterschätzter Bereich sind Compliance-Risiken. Wird beim Umzug gegen Auflagen verstoßen, drohen rechtliche Konsequenzen. Beispielsweise müssen beim Heben von Lasten mit Kran die Vorschriften der DGUV (Deutsche Gesetzliche Unfallversicherung, früher BGV) eingehalten werden – ein Verstoß, etwa durch nicht geprüfte Anschlagmittel, kann im Schadensfall den Versicherungsschutz kosten. Ebenso verlangt die Betriebssicherheitsverordnung, dass Maschinen vor Wiederinbetriebnahme auf sicheren Zustand geprüft werden. Hier drohen Bußgelder oder Stilllegungsverfügungen, wenn man es versäumt, eine prüfpflichtige Anlage (z. B. Krananlage, Druckbehälter) von einer befähigten Person abnehmen zu lassen. Das Risikomanagement führt daher Checklisten für Compliance: Sind alle benötigten Prüfungen, Abnahmen und Genehmigungen eingeplant? Wurden Arbeitsfreigaben (Permit-to-work) eingeholt für gefährliche Arbeiten wie Schweißarbeiten beim Wiederaufbau? Auch Umweltaspekte gehören hierher: Beim Transport von Maschinen mit ölhaltigen Teilen besteht Risiko von Leckagen – folglich sind Auffangwannen oder Abdichtungen vorzusehen und eine eventuelle Einstufung als Gefahrgut (z. B. bei mit Öl gefüllten Hydraulikaggregaten) zu prüfen.
Personalrisiken: Der Umzug belastet auch die Belegschaft – Schichtarbeit, ungewohnte Aufgaben, Reisearbeiten können erforderlich sein. Es besteht Unfallgefahr (Arbeitsschutz) und das Risiko von Know-how-Verlust, wenn z. B. Schlüsselpersonen ausfallen. Dem begegnet man durch intensive Arbeitsschutzmaßnahmen (Unterweisungen, Sicherheitsfachkräfte vor Ort, Einhalten von Ruhezeiten) und durch Wissenssicherung (Dokumentation und Austausch, sodass nicht eine Person allein kritisches Wissen hat). Pandemiebedingte Aspekte (wie plötzliche Quarantäne ganzer Teams) sind in jüngster Zeit ebenfalls Teil der Personalrisiken, hier helfen Notfallpläne und redundante Teamaufstellungen.
Zentraler Bestandteil der Risikoabsicherung ist eine detaillierte Dokumentation und Qualitätsprüfung an jeder Schnittstelle. Dies führt zum zweiten Aspekt, der Qualitätssicherung. Ein Maschinenumzug wird am besten so gehandhabt, als würde man einen Neubau einer Anlage durchführen – mit definierten Qualitätsschritten bei Abbau, Aufbau und Inbetriebnahme. In vielen Fällen erstellen Unternehmen spezifische Checklisten und Prüfprotokolle für Umzüge. Beispielsweise wird nach der Demontage ein Checklisteneintrag gemacht: "Sind alle Kabel so beschriftet, dass eine eindeutige Zuordnung möglich ist?" – abgehakt durch den verantwortlichen Techniker. Oder nach der Remontage: "Maschine mechanisch ausgerichtet gemäß Richtlinie XY? Wertprotokoll angehängt." – dokumentiert mit Messwerten. Die Anforderung an Dokumentation, Kalibrierung, Abnahmen und Prüfnachweise ist nicht nur bürokratischer Natur, sondern dient der Absicherung, dass keine wichtigen Schritte übersehen wurden. Es gilt: Was nicht geprüft und dokumentiert ist, ist nicht getan. Daher werden Prüfungen wie elektrische Sicherheitsmessungen, Achsgenauigkeitsmessungen, Funktionschecks etc. stets mit Datum, Uhrzeit und Verantwortlichem festgehalten und – falls erforderlich – von einem zweiten Fachmann gegengezeichnet (Vier-Augen-Prinzip bei sicherheitsrelevanten Funktionen).
Das Qualitätsmanagement nach ISO 9001 stellt dabei einen hilfreichen Rahmen: Ein nach ISO zertifiziertes Unternehmen wird einen Maschinenumzug als Änderung im Produktionsprozess verstehen und entsprechend dem Kapitel "Operation" und "Change Control" behandeln. Das bedeutet, alle Änderungen müssen geplant, verifiziert und validiert werden, um die Produktqualität nicht zu gefährden. Die ISO 9001 fordert zudem die Überwachung von Messmitteln – hierzu zählt auch, dass nach einem Umzug alle Messsysteme einer Maschine (Sensoren, Messdorne etc.) ordnungsgemäß funktionieren und kalibriert sind. Auch Schulungsanforderungen (ISO 9001 Kapitel "Kompetenz") spielen hinein: Mitarbeiter müssen nach dem Umzug ggf. neu eingewiesen werden, was im QS-Plan berücksichtigt wird.
Es ist anzumerken, dass professionelle Dienstleister in diesem Bereich ein eigenes Qualitätsmanagement betreiben und oft zertifiziert sind (viele sind z. B. ISO 9001:2015 zertifiziert). Sie bieten Leistungen "aus einer Hand" an, einschließlich Qualitätssicherung und aller nötigen Prüfungen, sodass der Auftraggeber am Ende eine laufende Maschine mit Prüfnachweisen übernimmt. So wurde etwa im beschriebenen Beispielprojekt jede Anlage nach Remontage mit modernen kalibrierten Messsystemen komplett ausgerichtet und sofort für die Produktion freigegeben. Die Kosten- und Zeitfaktoren sowie alle sicherheitstechnischen Vorschriften hatte der Dienstleister dabei ständig im Blick und konnte durch exakte Planung und professionelle Koordination die vorgegebenen Termine einhalten. Dieses Vorgehen illustriert, wie Risiko- und Qualitätsmanagement Hand in Hand gehen: durch Prävention, Prüfung und Dokumentation werden Risiken minimiert und die Qualität der Umsetzung sichergestellt.
Normen und Standards
Bei der Verlagerung von Maschinen sind zahlreiche Normen, Richtlinien und Vorschriften zu beachten, die sowohl die technische Ausführung als auch die organisatorischen Prozesse betreffen.
Im Folgenden ein Überblick über wichtige Regelwerke in diesem Kontext:
VDI-Richtlinien: Verschiedene VDI (Verein Deutscher Ingenieure)-Richtlinien geben Orientierung für Planung und Durchführung von Fabrikumzügen. Zum Beispiel bietet VDI 5200 Leitlinien für die Fabrikplanung, die auch auf Umstrukturierungen und Verlagerungen anwendbar sind (Planungsvorgehen in Phasen). Speziell für den Transport relevant ist VDI 2700, die umfangreiche Regeln zur Ladungssicherung auf Straßenfahrzeugen enthält – essentiell für Schwertransporte, um Unfälle und Schäden zu vermeiden. Weitere VDI-Richtlinien betreffen etwa Arbeitsplatzgestaltung bei Umbauten (Ergonomie) oder Anlaufmanagement nach Reorganisation, die im Einzelfall herangezogen werden können. Auch im Bereich Technische Dokumentation gibt es mit VDI 2770 einen Standard, der für digitale Maschinen-Dokumentationen genutzt wird und somit bei der geordneten Übergabe aller Unterlagen nach Umzug hilfreich sein kann.
DIN- und EN-Normen: Zahlreiche DIN-EN-Normen stellen den Stand der Technik für Maschinen und deren Installation dar. Wichtig sind hier z.B. DIN EN 60204-1 (VDE 0113-1) für die elektrische Ausrüstung von Maschinen – sie legt u. a. Anforderungen an die Wiederinbetriebnahme nach Änderungen fest (Kennzeichnung der Leitungen, Schutzerdung, Prüfen der Sicherheitsfunktionen). DIN EN ISO 12100 behandelt die allgemeine Maschinensicherheit und fordert eine Risikobeurteilung, was auch bei Standortänderungen relevant ist (Änderung der Nutzungssituation kann neue Risiken mit sich bringen). In bestimmten Branchen greifen zusätzlich Spezialnormen: z. B. DIN 24420 für Pressensicherheit oder Normen für die Aufstellung von Werkzeugmaschinen (wie ISO 230-Reihen für Genauigkeitsprüfung). Für Kalibrierungen sind Normen der ISO 230-Serie relevant (Mess- und Prüfverfahren für Werkzeugmaschinen). Falls bauliche Änderungen an Hallen nötig sind, kommen Bau- und Brandschutznormen ins Spiel (DIN-Normen für Fundamentbau, Statik etc.). Diese Vielfalt zeigt, dass je nach Umzugsprojekt eine spezifische Normenrecherche erfolgen muss, um alle anwendbaren Bestimmungen einzuhalten.
DGUV-Vorschriften: Hierbei handelt es sich um die Unfallverhütungsvorschriften der Berufsgenossenschaften, heute unter DGUV (Deutsche Gesetzliche Unfallversicherung) geführt.
Einige wesentliche Vorschriften sind:
DGUV Vorschrift 1 (ehem. BGV A1): Allgemeine Grundlagen des Arbeitsschutzes – fordert u.a. Gefährdungsbeurteilungen und Unterweisungen, was auf alle Umzugsphasen anzuwenden ist.
DGUV Vorschrift 3 (ehem. BGV A3): Elektrische Anlagen und Betriebsmittel – verlangt die Prüfung von elektrischen Maschinen nach Instandsetzung, Änderung oder Umzug, bevor sie wieder in Betrieb gehen. Somit ist ein E-Check Pflicht, wie oben beschrieben.
DGUV Regeln und Informationen: Z.B. DGUV Regel 100-500 enthält Kapitel zum Transport von Lasten mit Kranen, DGUV Information 209-073 gibt Hinweise zum Einsatz von Hydraulikhebern etc. – all das sind quellenspezifische Dokumente, die Sicherheit beim Heben und Bewegen schwerer Lasten gewährleisten sollen.
Branchenbezogene Vorschriften: Etwa BGHM (Holz- und Metall) spezifische Regeln, die beim Umgang mit bestimmten Maschinen gelten (z.B. UVV für Pressen, die auch nach Standortwechsel auf Sicherheit geprüft werden müssen).
ISO-Standards (Managementsysteme): Neben ISO 9001 für Qualitätsmanagement können auch ISO 45001 (Arbeits- und Gesundheitsschutz-Management) und ISO 14001 (Umweltmanagement) relevant sein. ISO 45001 fordert strukturiertes Vorgehen bei Arbeitsschutz, was perfekt in ein Umzugsprojekt integriert werden kann (Gefährdungsbeurteilungen, Notfallpläne etc.). ISO 14001 würde nahelegen, die Umweltaspekte des Umzugs zu betrachten – z.B. Entsorgung von Altmaterial, Vermeidung von Leckagen, Lärm- und Emissionsschutz beim Transport. Für bestimmte Branchen gibt es zudem GMP-Regeln (Good Manufacturing Practice), die verlangen, dass bei Standortverlagerung von Anlagen die Prozesse neu validiert werden. In der Pharmaindustrie etwa muss nach einem Umzug eine erneute Qualifizierung der Maschine erfolgen, bevor wieder produziert werden darf – dies fußt auf internationalen Leitfäden (wie FDA CFR21 oder EU GMP-Leitfaden) und entsprechenden ISO-Normen (z. B. ISO 13485 für Medizintechnik).
Es sei hervorgehoben, dass die Einhaltung dieser Normen und Standards nicht nur aus rechtlicher Sicht wichtig ist, sondern auch wesentlich zur Qualität und Sicherheit des Umzugs beiträgt. Sie stellen bewährte Best Practices dar. Unternehmen, die regelmäßig Maschinenverlagerungen durchführen, haben meist interne Standards entwickelt, oft basierend auf diesen Normen, um jeden Umzug strukturiert abzuwickeln. Dazu gehören z.B. firmeneigene Checklisten, die an ISO/VDI-Vorgaben angelehnt sind, oder Verträge mit Dienstleistern, die explizit die Erfüllung bestimmter Normen fordern. Letztlich dienen Normen und Standards als Richtschnur, damit kein wichtiger Aspekt übersehen wird – seien es technische Details, Sicherheitsvorkehrungen oder Dokumentationspflichten.